
White Wood Spruce lumbers present a straight grained light wood with uniform texture that is largely attributed to slow and consistent growth patterns. As a result, White Wood Spruce lumbers have the highest weight to strength ratio making it an attractive solution for both interior and exterior construction work, including boat building. Closely knit fibers of White Wood Spruce give it the ability to stand up to the elements and present well as an outdoor siding or on decks and balconies.
The unique composition of white White Wood Spruce is ideal for basic construction and specialized applications requiring exceptional acoustic properties such as wall panelling and is extensively used in the construction of pianos, guitars, violins and other musical instruments where acoustical properties are an integral part of engineering.
Its buoyant properties and lightness makes it the first choice of any engineered application where performance value is paramount.
Working Properties of White Wood Spruce
Availability options of White Wood Spruce
Hand selected and re-graded lumbers are generally available in following cross sections in several lengths, kiln dried to a maximum of 18% moisture content and surfaced on all four sides with edged edges.
18mm x 100mm
19mm x 90mm/140mm
21.5mm x 105mm/110mm
22mm x 100mm
27mm x 105mm/120mm
30mm x 105mm/120mm
38mm x 89mm/140mm/150mm/200mm/225mm
45mm x 90mm/95mm//105mm/120mm/204mm
50mm x 150mm/200mm
63mm x 150mm/200mm
Other dimensions can also be made available with prior arrangement
Grading Rules of Lumbers
International trade in Coniferous Lumbers is regulated by several regional standards followed in the areas where wood is grown and/ or harvested in the backdrop of its most common use as structural member in the housing and buildings taking in to account the need to grade the lumbers on a scale of several falling down levels so as to identify the portion pf wood that is suitable or recommended for structural uses of such graded wood.
The most common standards on grading of the sawn wood described as sawn timber or lumbers followed throughout the world with some variations in nomenclature or values is Nordic grading rules that classifies the sawn wood on scale of 0 to VII based on defects and appearances. Swedish Forest Industries Federation has published the Gradingof sawn timber in Europe according to EN 1611-1 which contains Terms and definitions,methods of measurementand requirementsin sawn timber according to EN-1611-1.
Broadly of seven levels designated to sawn lumbers, I-IV, U/S grade as mixture between I to IV or a lump of A1, A2, A3 and A4 in varying proportion, suitable for use as structural members in Home or building or applications where both appearance and minimum strength is necessary. Further falling down grades such as V or B, VI or C and VII or D and rejectshaveseveral other applications such as packaging, dunnage in vessels and containers, fencing, construction sites, Block Board and Flush Door fillerbesides host of other general purposes etc., In addition, such downgrades are cut to shorter lengths to remove the defects and finger jointed again to upgrade its values and used in manufacture of Glulam and other Laminated timbers, panelling, edge glued boards, flooring and parquets etc.
Eximcorp maintains sufficient inventory of Grade A or I-IV or US lumbers for select applications.
The rules that classify the sawn wood in scale of I to VII are detailed in the download section of this page with photos to understand the differences between the several grades.
Few illustrative photos are placed here under for ready reference.
Nordic Timber Grading
A=U/S grade (a mixture between A1 – A4)
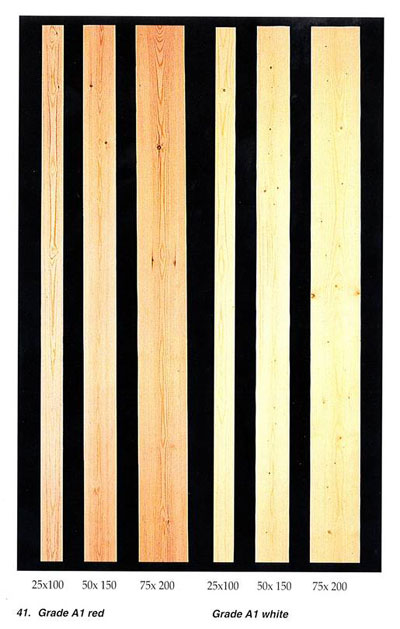
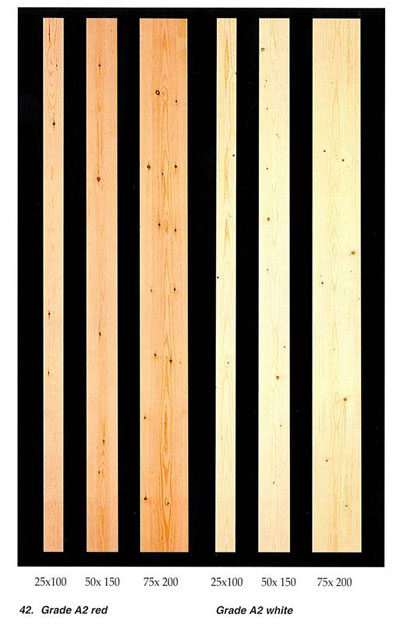
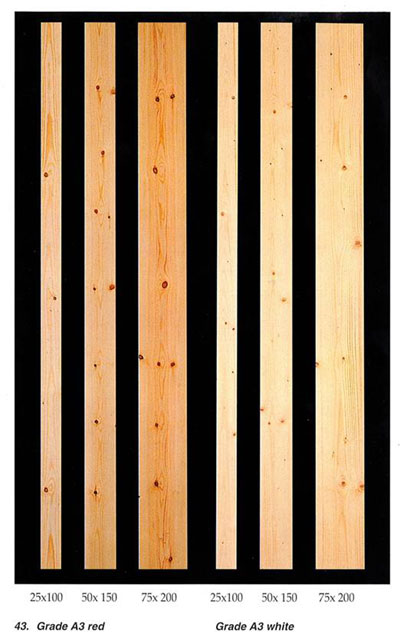
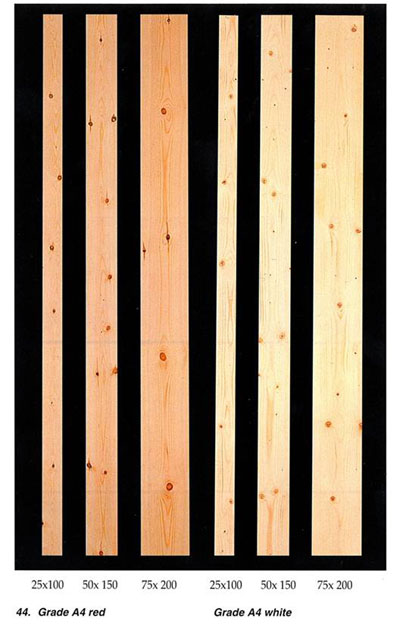
Nordic Timber Grading
B=5TH grade
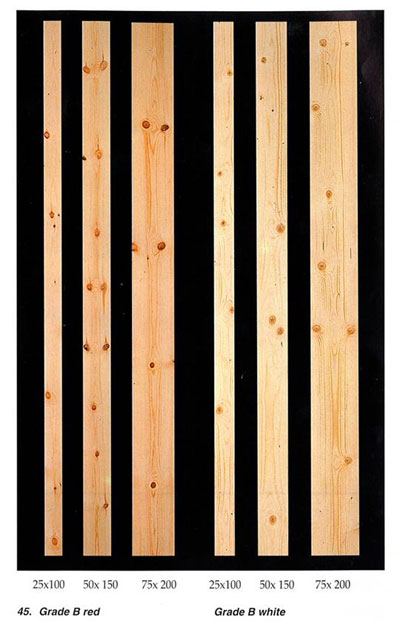
Nordic Timber Grading
C=6TH grade
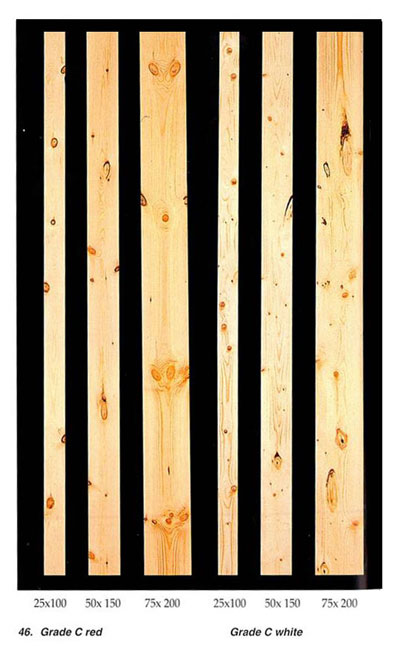
Common Defects in Sawn Timber (Lumbers)
Wood being a forestry product exposed to vagaries of nature, it is natural to have defects in wood but, since the wood is the most useful natural gift to mankind, every bit and portion has some application regardless of the nature and extent of defects. However, Eximcorp demonstrates by way of Photo certain common defects, that should not be used in any structural application where functional requirement in wood affects its performance particularly stability of the object.
No tree is perfect. It’s subject to defects from the time it emerges as a seedling to the last stages of Seasoning/drying. A defect is simply an abnormality or irregularity found in wood. There are many different types of defects arising from many different causes. For instance, there are natural and acquired defects caused by a broken limb or other injury, insect and fungal attack, or rapid tree growth. There are innate defects caused by the natural characteristic of wood to shrink or expand in response to water vapor in the air. And, there are artificial and mechanical defects caused by incorrect sawing or machining (conversion), improper drying (seasoning), or improper handling and storage. Defects may be responsible for reducing wood’s economic value, lowering its strength, durability and usefulness, marring its appearance, and in some cases, causing its decay.
Defects in Sawn Timber (Lumbers)
during kiln drying process
1. Bow
When the converted timber is stored for a longer time, some timber planks may have a curve along its length without sufficient block support, which is known as Bow.
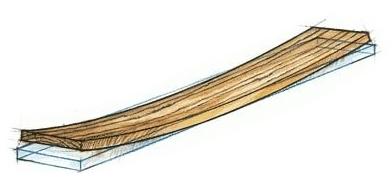
2. Cup
If the timber planks curve along its width, then it is called Cupping of timber.
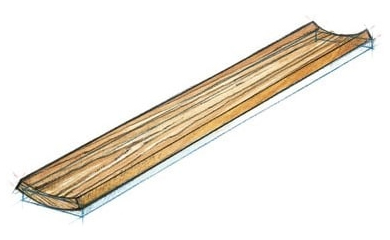
3. Check
Check is the formation of a crack in the wood, which will separate the wood fibers. They form due to over seasoning of timber.
4. Split
Split forms when a check extends from one end to the other end, which will split the wood into a number of pieces.
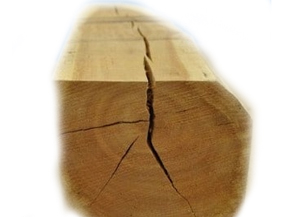
5. Twist
Twist forms when the timber piece is distorted spirally along its length. It looks like a propeller blade after twisting.
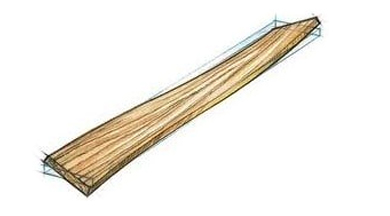
6. Honeycombing
Honey combing occurs in the inner part of the timber, which cannot be identified by just seeing. It is mainly due to stresses developed during the drying of timber.
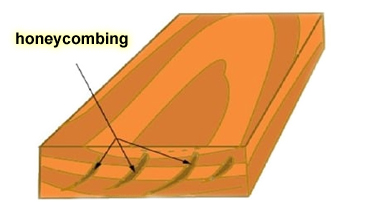
7. Case Hardening
Case is nothing but the top surface of wood, which dries rapidly during seasoning, but the inner part didn’t. Then this defect is called as case hardening.
8. Collapse
During drying, some parts of the wood may dry rapidly while some may not. Because of this, improper drying shrinkage of wood occurs, that results in the defect called collapse.
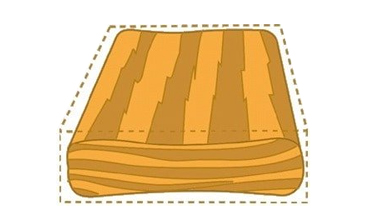
9. Warp
Warping is the loss of shape of wood due to stresses developed during drying. Cupping bowing, twisting of wood come under warping.
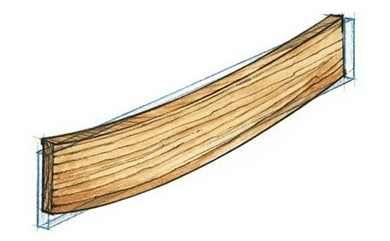
10. Radial Shakes
Radial shakes develop after the tree being felled down and exposed to the sun for seasoning. In this case, the cracks run radially from bark to the pith through annual rings.
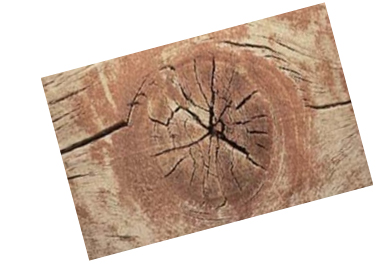
Wood defects during sawing
1. Diagonal Grain Defect in Timber
During the conversion of timber, different cutting saws are used. The cutting should be done properly. If there is any improper cutting by the saw, then a diagonal grains will appear.
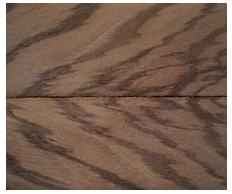
2. Torn Grain
In the conversion, many tools are used. If any of the tools or any other heavy things are dropped accidentally on the finished surface of timber it will cause small depression, which is called torn grain.
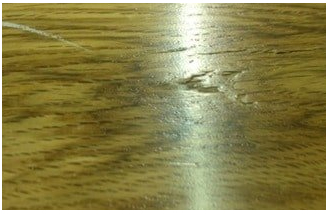
3. Chip Mark
When the timber is cut through the planning machine, the parts of the machine may form chip marks on it. Usually, they are indicated by chips on the finished surface.
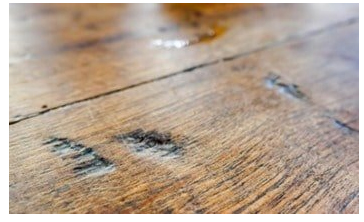
4. Wane
The edge part of the timber log contains a rounded edge on one side because of its original rounded surface. This rounded edge is called wane.
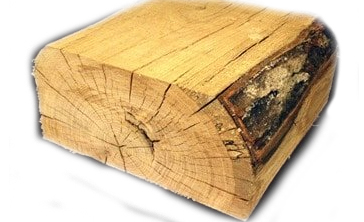
5. Slope of Grain
Localised slope of grain can be caused by knots. Slope of grain can also be caused by a slight bend in the tree, which means that when a straight board is cut out of it, there is a bend in the grain. This tends to be a longer feature and may go unnoticed in an appearance product.
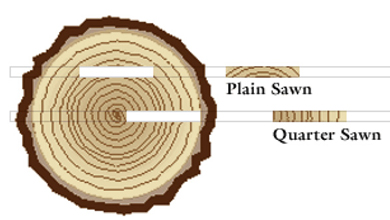
Some species of Australian hardwoods (such as Jarrah and Blackbutt) can have “wavy grain”. This gives a very attractive rippled appearance in high surface finish applications.
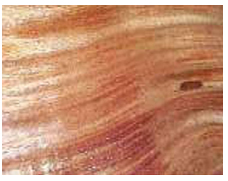
Where timber is “backsawn”, the slope of grain can give interesting effects in the growth rings that enhance the appearance of the timber for some applications.
Defects in timber due to Insects
1. Termites in Timber
Termites also known as white ants which form a colony inside the timber and eat the core part of the timber rapidly. They do not disturb the outer layer of timber, so one cannot identify their presence. The trees in tropical and sub-tropical regions are mostly affected by these termites. However, some trees like teak, Sal, etc. cannot be attacked by termites because of the presence of termite preventing chemicals in their cellulose part.
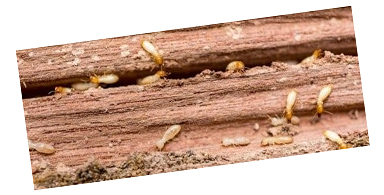
2. Beetles in Timber
Beetles are a type of insects that destroy the sapwood of the tree and make a tunnel-like hole from the bark. Usually, the diameter of the hole is around 2 mm. They convert sapwood into powder form, and larvae of these beetles use these holes. Almost all hardwood trees can be prone to damage by these beetles.
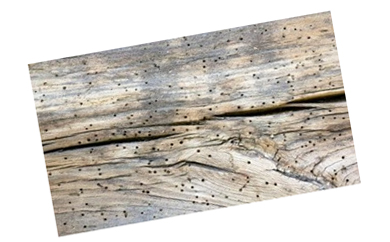
3. Marine Borers in Timber
Marine borers are found near coastal areas. They do not consume wood, but they make large holes of diameter up to 25mm in the timber to live inside it. They excavated up to 60mm deep in the wood. The wood attacked by marine borers is of less strength and discolored. They can attack all types of trees present in their region.
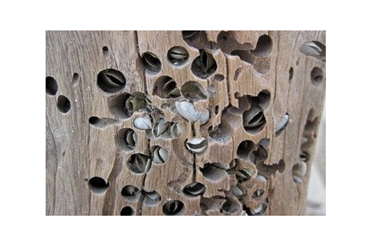
Preservatives
All Lumbers and Beams are made from natural wood logs grown and harvested in the country of its origin and is free from any toxic chemicals treatment as preservative. As is common knowledge, all wood products are susceptible to insects or termites and/or borers present in different climatic zones in the soil or buildings. It is recommended that the users are applying the coat of suitable chemicals or insecticides on all exposed surfaces of wood in addition to treatment of masonry foundations of the building where the Wood products are required to be use. Fipronil emulsified concentrate at about 3% is one such chemical and effective deterrent against insects and pests or termites in tropical climate zones. However, the application should be in accordance with manufacturers guidelines for effective results. Users own discretion in selection of appropriate chemical and its doses or frequency of such treatment is advised for satisfactory results in the light of experience gained over the period of time.